MQL 411: Ecologically Friendly, Minimum Quality Lubrication Saves Time and Money
Minimum Quantity Lubrication (MQL), or near-dry machining has been around for almost two decades. Recently it has seen a resurgence in use and is replacing flood coolant and dry machining. Research demonstrates that the process can save money, time and the environment, if used properly.
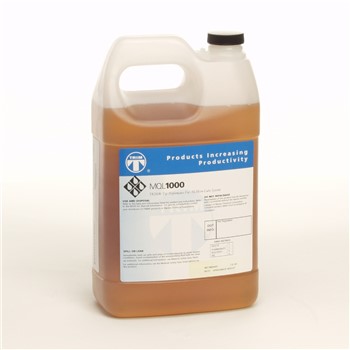
MQL Definition
This process can be used in two ways. One is the lubricant is delivered through the tool with a properly equipped spindle and tooling. While this is an option that some shops adopt, the most popular application is delivering a vegetable-based lubricant through external nozzles. The precise aim of these nozzles is vital to the process. While flood coolants can hit the tool within an inch and still be effective, the MQL microdroplets must be within a millimeter of its target. If the flow misses, then machining near-dry becomes average machining dry.
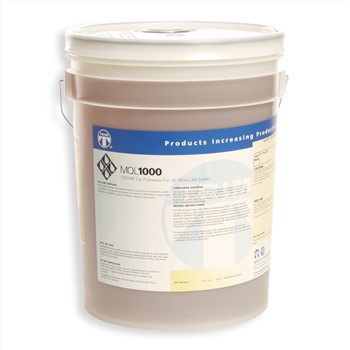
MQL Uses Less Coolant
According to Optis, a joint venture between TechSolve and Castrol, flood coolant uses as much as 60,000 ml of fluid per hour, while MQL typically uses less than 500 ml per hour. Essentially it cuts fluid use to ounces instead of gallons. The Optis research further states that the effective use of MQL can cut fluid costs by as much as 15%. MQL is also versatile. The process can be used for: turning, milling, drilling, circular and band sawing, reaming, tapping, routing and broaching.
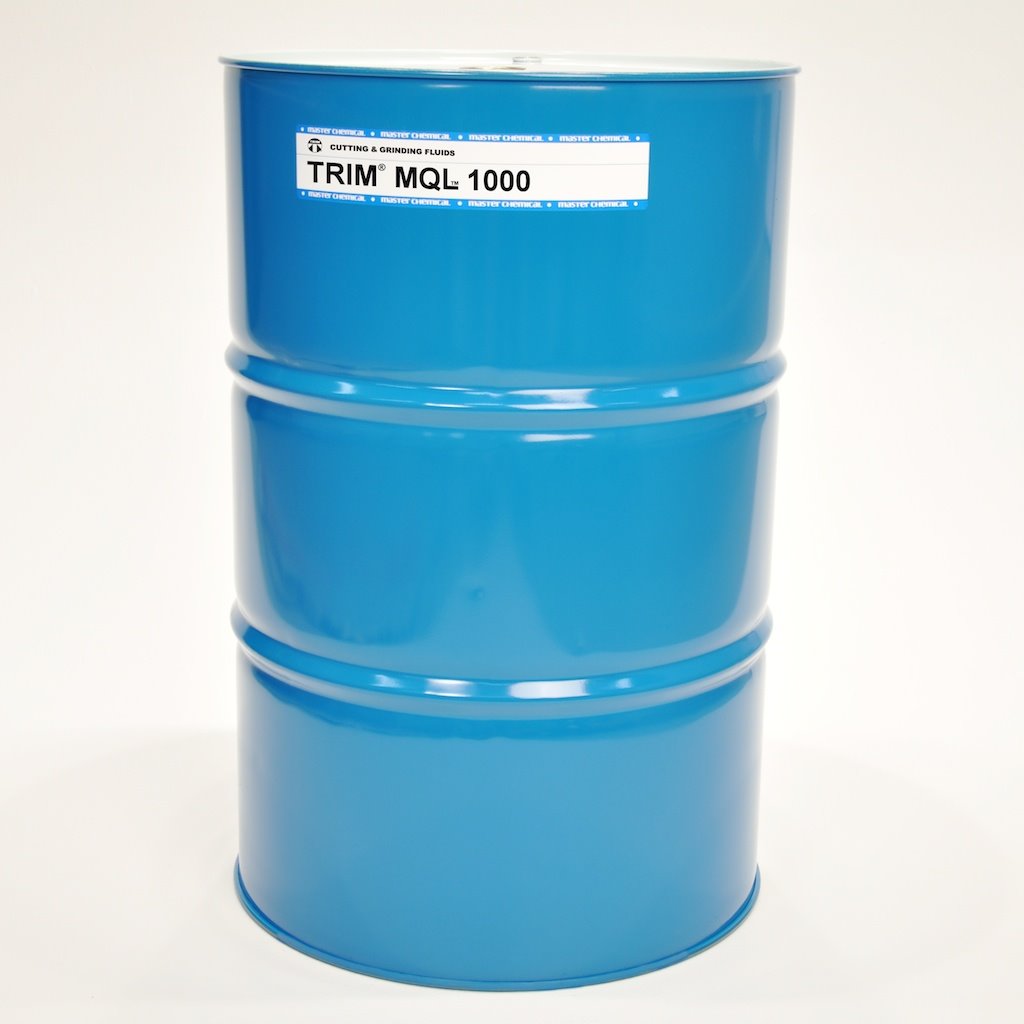
MQL Benefits
MQL technology was created to be a viable option to replace flood fluid systems. As stated above, MQL uses less fluid and cost less to implement. Other benefits of using properly applied MQL have been shown to include:
- Reduce tool wear - Reported cases have shown an increase in tool life of 50 to 100 percent.
- Increase in consistency and integrity of machined surface – Projects have shown a more consistent finish and less residual stresses.
- Dryer and cleaner chips - Reduced fluid splashing results in a longer life for Sensor switches, cleaner machines and less shop mess.
- A cleaner, greener alternative - The cost of buying and disposing of conventional cutting fluids is reduced, and less energy is consumed
- Reduce toxic waste - Less use of cutting fluid results in a cleaner and healthier shop environment.
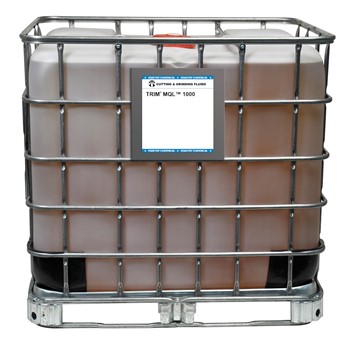
MQL Disadvantages
It seems that MQL is the wave of the future, but before you make the change consider some of its disadvantages:
- Not appropriate for deep-hole drilling, energy-intensive processes such as grinding, special operations like honing and small-hole drilling, or for difficult-to-machine materials such as titanium and nickel-based alloys.
- The ultra-fine mist produce by the MQL process can be more difficult to filter.
- Implementation may entail changing the machine tool and processing strategy.
- Does not match the chip evacuation abilities of wet machining.
In the end it’s up to you, but BlackHawk Industrial can help you with your decision. Let our trained professionals at BlackHawk Industrial help you with your lubrication application questions.
We welcome you to contact us here https://www.bhid.com/ContactUs or call us TOLL FREE at (855) 610-1001. You can also check out our website at https://www.bhid.com/.